Wanhao D6 nozzle update
I would like to call the reader’s attention to the fact that the implementation of the following will certainly result in loss of warranty, and incorrect installation may cause damage to the device! In case of uncertainty or lack of technical affinity, please contact us with confidence.
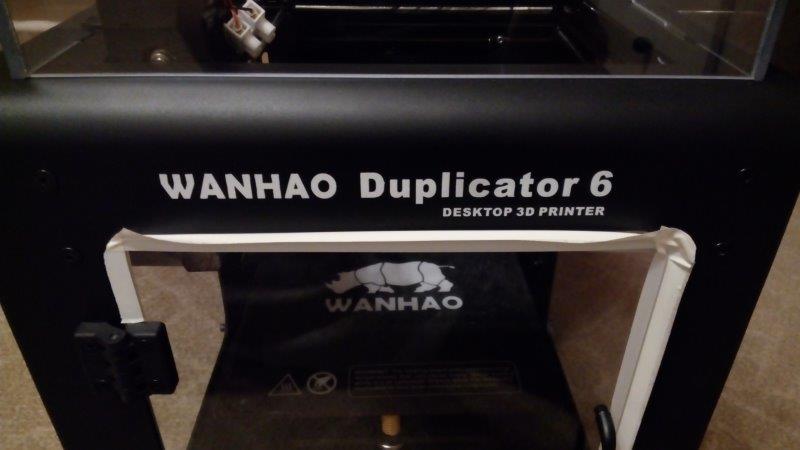
What do we win by changing the head (nozzle)? This is the most important question during such a transformation. Several inquiries were made regarding elements where both detail and small size were important to the Customer. Here we can think of a piece of jewelry or the basis of a dental implant (a basis from an implant, which is a 1:1 copy of the patient’s oral cavity and the tooth or dental bridge is made from this pattern). As all tools, the Wanhao D6 printer has got the technical limitations. In our case, we gain the increase in resolution at the expense of printing time. What does it mean? The layer thickness is given between 0.1 and 0.05 mm; as long as we work with a 0.4mm head, the fiber thickness that can be laid in one line is ~0.5mm. The head must pressed the layers together, because the bond will be weak and the printed object will break.
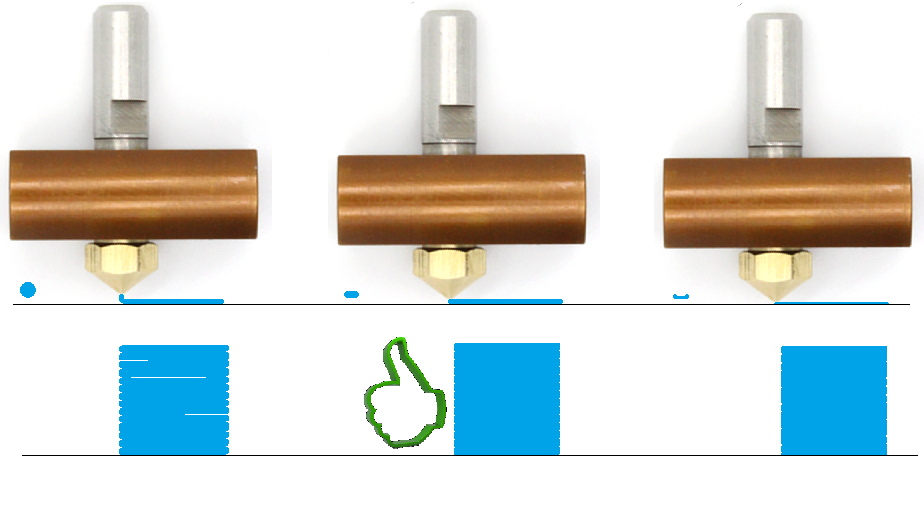
With these data, it can be seen that the scale on the vertical side can be controlled by prepressing the filament. The resulting scale is regulated between 0.1 and 0.05. On the other hand, the horizontal scale can’t physically be smaller than 0.5 mm. For the strength of the layers, the thinnest material thickness is therefore 0.7mm. The resulting resolution is between 0.1×0.7mm. We can notice that the resolution of 0.05×0.7mm does not make sense, we call this a marketing catch! But why did we mention this? Well, because of the time. Due to the head size of our printer (0.4mm) and the speed of the stepping motors (25 mm/s), we will have a printing time. Ergo, the slower we print, the higher the resolution we will print. This means that if we change the head from 0.4mm to 0.2mm, our resolution will be: 0.1×0.4mm. Considering the other technical parameters (speed, temperature, material type – ABS -); since they have changed minimally or not at all, the printing of the same object takes more time than before when using the 0.4mm head; but the resolution is almost we were able to double it. For example, in the case of a cube, which used to take 3-4 hours, it now takes 5-6 hours.
Then let’s get started with the above in mind.
1., Heat the head (nozzle) to at least 190°C.
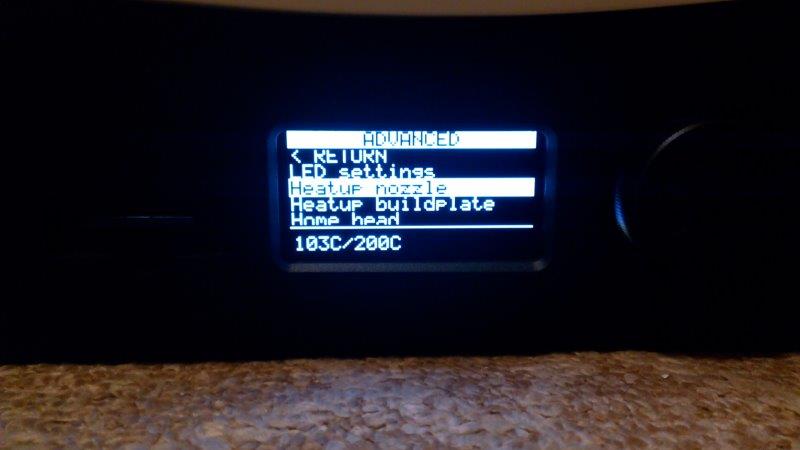
2. Take out the filament.
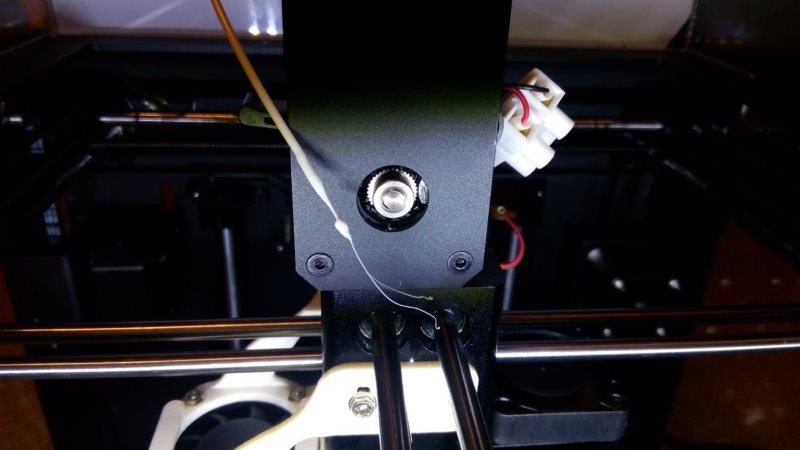
3. Unscrew the screws holding the head.
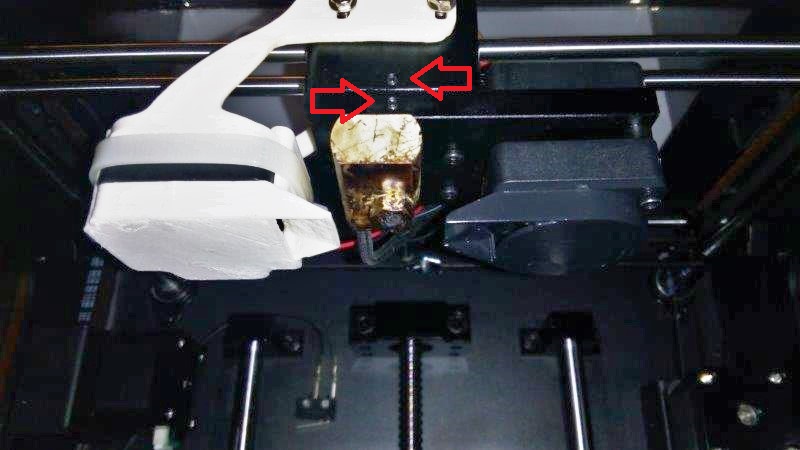
4. Before lifting out the head, turn it to the left, then the two screws that hold the heating cartridge and the thermocoupler will be visible on the „hotend”. After removing the heating cartridge and thermocoupler, lift out the head.
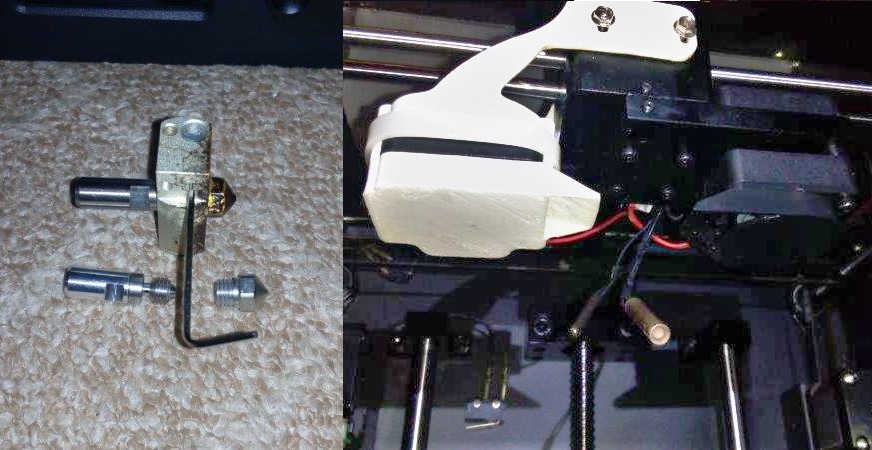
5. Replace the head and the filament. We should pay attention to three things: one, stay a fix position the hotend, thus preventing us from tearing the screw thread and not even scratching the hotend; second, before putting the head and stem (Guiding Tube) together, clean the hotend with a wire brush; and finally, wrap the nozzle first in the hotend and then screw in the stem (Guiding Tube). Pull it properly, because the soft filament easily comes out next to the holes, and from there we can only clean and disassemble it by heating it to 190°C.
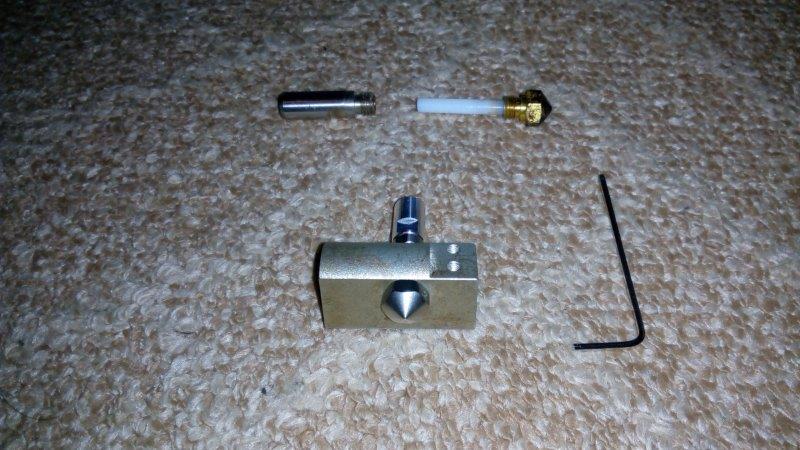
6. Install the head in place, but do not tighten the screw. There is a screw at the left rear of the tray, lift the tray until it is fully up. Then the head can be released, because it will not be able to fall out of the tray. If the head gets stuck in the tray, lower the tray and adjust the screw so that the limit switch is pressed. Fix the head in this position.
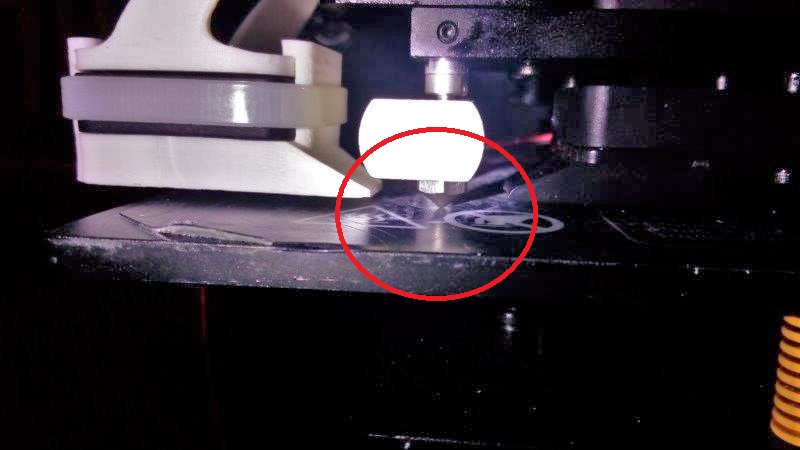
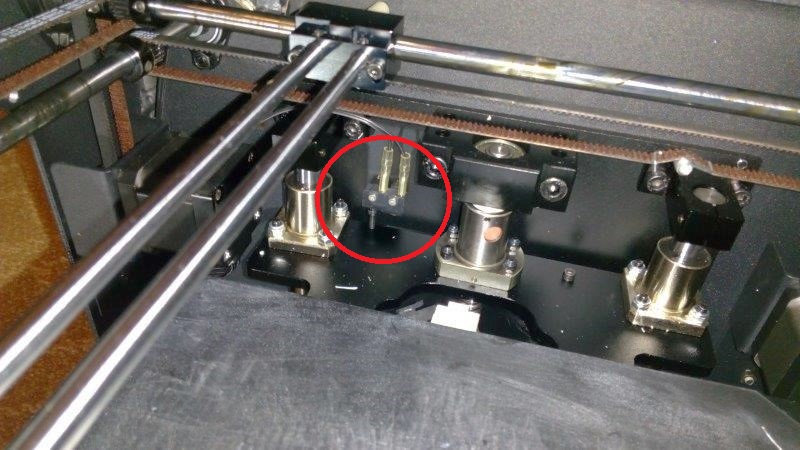
Thank you for reading!